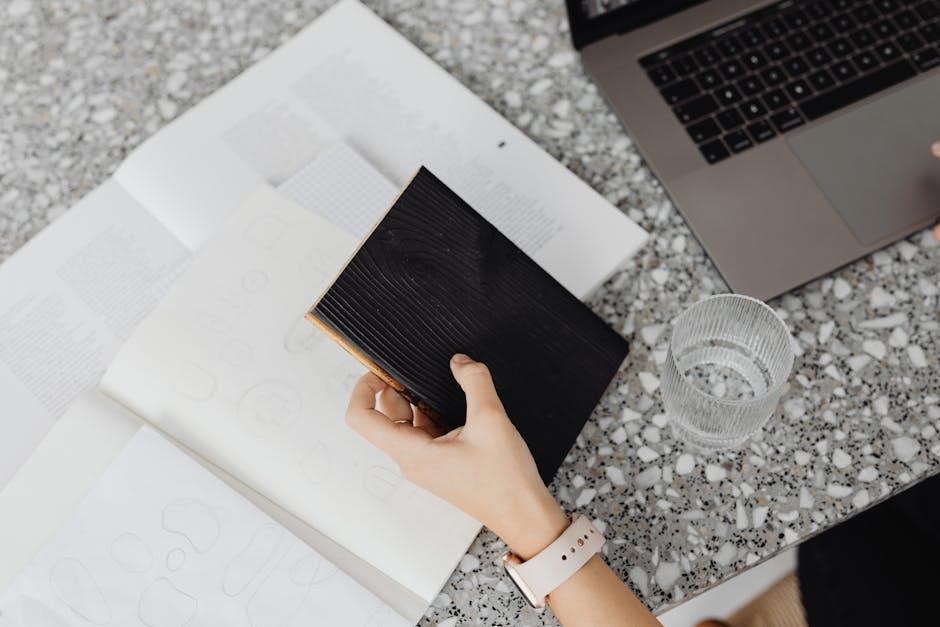
AS9102 is a globally recognized aerospace standard published by SAE International, outlining requirements for First Article Inspection (FAI) to ensure product quality and reliability.
1.1 What is AS9102?
AS9102 is a standardized requirement published by SAE International, detailing the process for First Article Inspection (FAI) in the aerospace industry. It ensures that the first production unit meets design specifications, quality, and reliability standards. The standard applies to all levels of the supply chain, providing consistent documentation and verification processes for aerospace, defense, and space products globally.
1.2 Historical Background of AS9102
AS9102, published by SAE International, originated to standardize First Article Inspection (FAI) processes in the aerospace industry. Initially introduced to ensure compliance with quality standards, it has evolved through revisions, with significant updates in 2000 (AS9102A) and 2014 (AS9102B). These revisions emphasized FAI’s value, enhanced planning, and incorporated Digital Product Definition (DPD). The standard aligns with global aerospace requirements, ensuring consistency and reliability across the supply chain.
1.3 Importance of AS9102 in the Aerospace Industry
AS9102 is critical for ensuring aerospace product quality, reliability, and compliance with global standards. It provides a standardized framework for First Article Inspection, verifying that design specifications are met. By emphasizing thorough documentation and evaluation, AS9102 enhances transparency and accountability, fostering trust among suppliers and customers. Its adoption is essential for maintaining safety, performance, and regulatory compliance in the aerospace sector, driving industry-wide consistency and excellence.
Key Features of AS9102
AS9102 emphasizes detailed documentation, rigorous inspection processes, and verification of design characteristics to ensure compliance and product quality in the aerospace industry.
2.1 Documentation Requirements for First Article Inspection (FAI)
AS9102 mandates comprehensive documentation for FAI, including detailed forms like Form 1 (Part Number Accountability) and Form 2 (Materials and Special Processes). These forms ensure traceability and compliance with design specifications. The standard requires thorough documentation to provide objective evidence that all engineering and specification requirements are met. FAI reports must be submitted as a single PDF, combining all relevant documentation for clarity and accountability.
2.2 Inspection Requirements for Aerospace Components
AS9102 specifies rigorous inspection requirements for aerospace components, focusing on design characteristics such as dimensions, materials, and functionality. Suppliers must ensure all parts meet specified requirements through detailed inspections. The standard mandates verification of design features, material properties, and functional testing to guarantee product conformity. These inspections are critical for maintaining the safety and reliability of aerospace systems, ensuring compliance with industry standards and customer expectations.
2.3 Design Characteristics and Their Role in FAI
Design characteristics, such as dimensions, materials, and functionality, are critical in FAI under AS9102. These features, defined by engineering drawings or Digital Product Definition (DPD), must be thoroughly inspected. They ensure the product meets design intent and specifications. FAI validates these characteristics, confirming that production processes can accurately replicate the design. This step is vital for ensuring product quality, reliability, and compliance with aerospace standards, making it a cornerstone of the FAI process.
The FAI Process According to AS9102
The FAI process under AS9102 involves structured planning, execution, and evaluation, with thorough documentation to verify product quality and compliance with aerospace standards.
3.1 Planning and Preparation for FAI
Planning and preparation for FAI involve defining objectives, identifying design characteristics, and preparing documentation. Organizations must ensure all requirements are understood and resources are allocated. This step includes reviewing designs, assigning responsibilities, and aligning processes with AS9102 guidelines to guarantee a smooth inspection process. Proper preparation ensures that the FAI is conducted efficiently and meets aerospace quality standards.
3.2 Execution of the FAI Process
The execution of FAI involves verifying that all design specifications and requirements are met. This includes conducting detailed inspections, testing, and documentation. Key activities involve verifying design characteristics, materials, and special processes. FAI forms, such as Form 1 and Form 2, are used to document findings. The process ensures compliance with AS9102 standards, providing objective evidence of product conformity and process capability.
3.3 Documentation and Evaluation of FAI Results
Documentation of FAI results involves completing standardized forms like Form 1 and Form 2, capturing all inspection and test findings. The FAI report is compiled, summarizing results and verifying compliance with design requirements. Evaluation ensures all characteristics meet specifications, and any non-conformities are addressed. The process concludes with approval or rework instructions, ensuring product quality and compliance with AS9102 standards before final acceptance.
Forms and Templates in AS9102
AS9102 provides standardized forms and templates for FAI documentation, including Form 1 for part accountability and Form 2 for materials, special processes, and functional testing.
4.1 Form 1: Part Number Accountability
Form 1 in AS9102 focuses on part number accountability, ensuring traceability of serialized parts. It includes fields for part number, serial number, FAI report number, and drawing revision level. This form is essential for tracking and verifying the integrity of aerospace components, ensuring compliance with design specifications and regulatory requirements. Its structured format aids in maintaining clear documentation throughout the supply chain.
4.2 Form 2: Product Accountability ― Materials, Special Processes, and Functional Testing
Form 2 addresses product accountability, focusing on materials used, special processes applied, and functional testing conducted. It ensures that all critical aspects of the product are documented and verified, providing a comprehensive record of compliance with design specifications; This form is crucial for maintaining transparency and accountability in the aerospace supply chain, ensuring that all components meet rigorous industry standards and customer expectations.
4;3 Other Supporting Forms and Their Purposes
Beyond Forms 1 and 2, AS9102 includes additional forms tailored to specific aspects of FAI. These forms cover detailed documentation of design characteristics, dimensional inspections, and process validations. They ensure comprehensive traceability and accountability, supporting the overall FAI process by providing structured data collection and verification methods. Each form serves a unique role in maintaining compliance and integrity throughout the aerospace product lifecycle.
Benefits of Implementing AS9102
AS9102 enhances product quality, reliability, and supply chain transparency while ensuring compliance with global aerospace standards, fostering trust and operational efficiency across the industry.
5.1 Enhanced Product Quality and Reliability
AS9102 ensures enhanced product quality and reliability by requiring rigorous First Article Inspection (FAI) processes. This standard mandates thorough documentation and verification of design characteristics, materials, and functional testing, providing objective evidence of compliance. By ensuring production processes are validated upfront, AS9102 minimizes defects, reduces variability, and improves overall product performance, aligning with global aerospace quality standards.
5.2 Improved Supply Chain Transparency
AS9102 enhances supply chain transparency by requiring detailed documentation and traceability of materials, special processes, and testing. This standard ensures accountability across all tiers of the supply chain, fostering collaboration and trust. By documenting every step, from design to delivery, AS9102 promotes clear communication, reducing risks and ensuring compliance with global aerospace standards.
5.3 Compliance with Global Aerospace Standards
AS9102 aligns with global aerospace standards, ensuring harmonization across international markets. It complements AS9100 and other IAQG standards, providing a unified framework for quality management. By adhering to AS9102, organizations demonstrate compliance with industry best practices, facilitating acceptance by global aerospace authorities. This standard supports the aerospace industry’s goal of maintaining consistent quality and reliability worldwide, reflecting its role as a cornerstone of international aerospace standards.
Challenges in AS9102 Implementation
Implementing AS9102 involves challenges such as complex documentation, resource-intensive processes, and the need for specialized training, which can strain organizational resources and require significant investment.
6.1 Common Issues Faced by Organizations
Organizations often struggle with AS9102 due to complex documentation requirements, resource-intensive processes, and the need for specialized training. Ensuring supply chain transparency and adapting to digital tools like DPD can also pose challenges. Compliance with evolving standards and maintaining consistency across global supply chains further complicates implementation. Additionally, small and medium-sized enterprises may face resource limitations, making it difficult to allocate sufficient time and expertise to meet AS9102 requirements effectively.
6.2 Strategies for Overcoming Implementation Challenges
Organizations can overcome AS9102 challenges by investing in comprehensive training programs and leveraging digital tools like FAI software. Establishing clear communication channels across the supply chain and adopting standardized processes ensures consistency. Regular audits and continuous improvement initiatives help maintain compliance. Collaboration with industry experts and utilizing resources from SAE International also supports successful implementation. Proactive planning and resource allocation are key to addressing these challenges effectively.
AS9102 and Compliance
AS9102 ensures compliance with global aerospace standards by standardizing FAI processes, aligning with AS9100, and meeting regulatory requirements for aviation, space, and defense products.
7.1 Regulatory Requirements and Industry Standards
AS9102 aligns with global aerospace standards, ensuring compliance with regulatory requirements for aviation, space, and defense products. It is technically equivalent to EN 9102 in Europe and SJAC 9102 in Asia, providing a unified approach to First Article Inspection (FAI). The standard complements AS9100 quality systems, emphasizing the importance of FAI in verifying design and production compliance with industry standards and customer specifications.
7.2 Ensuring Compliance in the Aerospace Supply Chain
AS9102 ensures compliance by standardizing FAI processes across the supply chain, promoting transparency and accountability. It mandates detailed documentation and traceability, enabling suppliers to verify adherence to design and regulatory requirements. This fosters trust and consistency, ensuring all components meet aerospace standards, ultimately safeguarding the integrity of the final product and maintaining compliance with global industry expectations.
Digital Transformation in AS9102
AS9102 incorporates Digital Product Definition (DPD), enabling digital transformation in FAI processes. This enhances documentation accuracy, streamlines inspection workflows, and improves efficiency across the aerospace supply chain.
8.1 The Role of Digital Product Definition (DPD)
DPD plays a critical role in AS9102 by providing a digital framework for design characteristics. This ensures precise, measurable, and repeatable FAI processes, enhancing traceability and compliance with aerospace standards. DPD integrates seamlessly with digital tools, improving data accuracy and accessibility. It supports the creation of detailed digital models, enabling real-time collaboration and reducing errors. This digital approach strengthens the overall reliability of FAI outcomes.
8.2 Leveraging Technology for FAI Documentation
Technology plays a pivotal role in streamlining FAI documentation under AS9102. Digital tools enable the creation, management, and submission of FAI reports in standardized formats, such as PDF. This ensures consistency, traceability, and compliance with aerospace standards. Automated systems reduce errors, while secure platforms facilitate collaboration across supply chains. The integration of digital solutions enhances the efficiency and accuracy of FAI documentation, supporting the overall quality assurance process.
Training and Certification for AS9102
Comprehensive training and certification programs ensure professionals understand AS9102 requirements, enabling effective implementation of FAI processes and ensuring compliance with aerospace standards.
9.1 Importance of Training in FAI Processes
Training in FAI processes is critical for ensuring compliance with AS9102 standards, promoting a deep understanding of documentation requirements, and fostering a culture of quality and accountability. Proper training enables professionals to accurately interpret design characteristics, execute inspections effectively, and maintain consistency across the supply chain. It also ensures that teams can identify and mitigate risks, contributing to the delivery of reliable aerospace products. Regular updates and certification programs further enhance proficiency in evolving standards and technologies.
9.2 Certification Programs for AS9102 Professionals
Certification programs for AS9102 professionals are essential for ensuring expertise in FAI processes and compliance with aerospace standards. These programs provide in-depth training on documentation, inspection requirements, and design characteristics. Certification enhances individual credibility and organizational competence, ensuring adherence to global aerospace standards. Professionals gain advanced knowledge of FAI execution, evaluation, and reporting, enabling them to lead quality initiatives effectively within the aerospace supply chain.
Case Studies and Success Stories
Real-world applications of AS9102 demonstrate its effectiveness in enhancing quality and compliance across aerospace projects, providing valuable insights into successful implementation strategies and industry best practices.
10.1 Real-World Applications of AS9102
AS9102 is widely applied in aerospace manufacturing to ensure compliance and quality. Companies use it for FAI processes, leveraging Form 1 for part accountability and Form 2 for materials traceability. Its integration with AS9100 enhances quality management systems, while digital tools streamline documentation. Successful implementations include major aerospace suppliers improving transparency and reducing defects, demonstrating the standard’s critical role in maintaining industry excellence and customer trust.
10.2 Lessons Learned from Successful Implementations
Successful AS9102 implementations highlight the importance of thorough planning, cross-functional collaboration, and robust training programs. Organizations have learned that early engagement with suppliers and clear communication of requirements are critical. Additionally, leveraging digital tools for FAI documentation and fostering a culture of continuous improvement ensure sustained compliance and quality. These lessons underscore the value of aligning processes with industry standards to achieve operational excellence and customer satisfaction.
Revisions and Updates to AS9102
AS9102C, revised in June 2023, enhances FAI planning, evaluation, and Digital Product Definition (DPD). Updates align with 9100 standards, addressing stakeholder needs and improving process clarity.
11.1 Key Changes in Recent Revisions (e.g., AS9102B to AS9102C)
The revision from AS9102B to AS9102C, issued in June 2023, emphasizes enhanced FAI planning, evaluation, and re-accomplishment activities. It introduces Digital Product Definition (DPD) and aligns requirements with AS9100 standards. Changes include improved definitions, streamlined documentation, and clarified inspection processes. These updates aim to address stakeholder feedback, ensuring better process efficiency and compliance with global aerospace standards. The revision also strengthens the focus on supply chain transparency and product quality assurance.
11.2 Impact of Revisions on the Aerospace Industry
The updates in AS9102C align the standard with AS9100, enhancing compliance and process consistency. The emphasis on Digital Product Definition (DPD) fosters innovation and efficiency. These changes streamline FAI processes, improve supply chain transparency, and reduce errors. By addressing stakeholder needs, the revisions promote global harmonization, enabling organizations to meet evolving industry demands while ensuring product quality and reliability for the aerospace sector.
Integration with Other Aerospace Standards
AS9102 aligns with AS9100 and other IAQG standards, ensuring a cohesive quality management system across the aerospace industry by harmonizing FAI requirements and processes globally.
12.1 Relationship with AS9100 and Other IAQG Standards
AS9102 complements AS9100 by providing detailed FAI requirements, ensuring alignment with IAQG standards. It integrates seamlessly with other aerospace quality systems, enhancing overall process consistency and compliance across the supply chain. This harmonization supports a unified approach to quality management, facilitating collaboration and reducing redundancy in documentation and processes for organizations adhering to IAQG standards.
12.2 Harmonization of FAI Requirements Across Standards
AS9102 ensures harmonized FAI requirements across global aerospace standards, including AS9100 and EN 9102. This alignment minimizes inconsistencies, enabling organizations to apply uniform processes worldwide. By standardizing documentation and inspection criteria, AS9102 facilitates compliance with multiple standards, reducing complexity and enhancing efficiency for suppliers and manufacturers across the aerospace industry.
Tools and Resources for AS9102 Compliance
AS9102 compliance is supported by software solutions for FAI documentation and reference materials like AS9102C standards, ensuring accurate and efficient implementation across aerospace organizations.
13.1 Software Solutions for FAI Documentation
Software solutions streamline FAI documentation by providing digital tools for tracking, reporting, and validating compliance with AS9102 requirements. These platforms ensure accurate data capture, real-time collaboration, and integration with quality management systems. Features include automated form generation, design characteristic validation, and compatibility with Digital Product Definition (DPD). Such tools enhance efficiency, reduce manual errors, and support organizations in maintaining regulatory compliance across the aerospace supply chain.
13.2 Reference Materials and Guidelines
Reference materials for AS9102 include official publications, guides, and training resources from organizations like IAQG and SAE. These documents provide detailed instructions for FAI processes, form completion, and compliance. They also offer checklists, templates, and industry examples to support implementation. Additionally, online courses and workshops are available to help professionals master AS9102 requirements and stay updated on the latest revisions and best practices in the aerospace sector.
Future Trends in AS9102 and FAI
Emerging technologies like AI and IoT will enhance FAI processes, while AS9102 will evolve to integrate digital product definition and advanced inspection methods, ensuring compliance and efficiency.
14.1 Emerging Technologies in Aerospace Inspection
Emerging technologies such as Artificial Intelligence (AI), Machine Learning, and the Internet of Things (IoT) are revolutionizing aerospace inspection processes. Advanced digital tools enhance First Article Inspection (FAI) by improving accuracy and efficiency. Predictive analytics and real-time monitoring enable early defect detection, reducing errors. Blockchain technology is also being explored for traceability and secure documentation. These innovations align with AS9102 requirements, ensuring compliance while modernizing quality control practices in the aerospace industry.
14.2 The Role of AS9102 in the Digital Age
AS9102 plays a pivotal role in the digital age by supporting the integration of Digital Product Definition (DPD) and advanced inspection tools. The standard aligns with Industry 4.0 initiatives, enabling seamless digital documentation and data exchange. It ensures compliance with modern quality systems while fostering innovation in aerospace manufacturing. AS9102’s digital transformation supports efficient, accurate, and traceable processes, making it indispensable for maintaining global aerospace standards in the era of smart manufacturing.
AS9102 is a cornerstone of aerospace quality assurance, ensuring components meet rigorous standards through First Article Inspection. Its evolution underscores its critical role in advancing industry reliability and compliance.
15.1 Summary of Key Points
AS9102 establishes requirements for First Article Inspection (FAI), ensuring aerospace components meet design and quality standards. It emphasizes documentation, inspection, and compliance, aligning with global aerospace standards. The standard fosters transparency, reliability, and innovation across the supply chain. Its evolution reflects industry needs, integrating digital tools and harmonizing with other standards like AS9100. AS9102 remains vital for maintaining quality and advancing aerospace manufacturing and technology.
15.2 The Evolution and Future of AS9102 in Aerospace
AS9102 has evolved to meet industry demands, with revisions like AS9102C enhancing digital integration and clarity. Future updates will likely focus on emerging technologies, such as AI and IoT, to optimize FAI processes. The standard’s alignment with global aerospace standards ensures its continued relevance, driving innovation and maintaining quality in aerospace manufacturing and supply chains for years to come.